
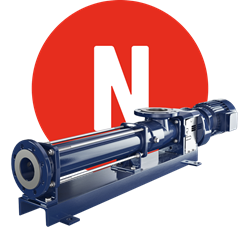
N - STANDARD PROGRESSIVE CAVITY PUMPS
The N module forms the robust basis for all SEEPEX progressive cavity pumps. It can pump low-viscosity to viscous media, with and without solids, and can be used in virtually all industries – from the environmental industry to the chemical industry and food production. The pumps are fitted with round flanged suction and pressure connections, as well as large spherical inlet openings for the simple intake of media that contain solids.
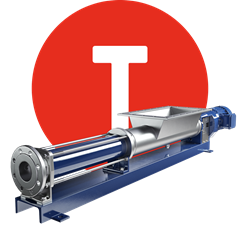
T - OPEN HOPPER PUMPS
-
SEEPEX open hopper pumps convey viscous to semi-solid products with low or no flowability. They are equipped with a feed hopper with a screw conveyor in order to optimally feed the product to the conveying elements. The pitch and diameter of the screw conveyor can be varied for different media, allowing optimal design for different applications. With ten ranges and numerous variations, we can fulfill the requirements of virtually all branches of industry.
-
-
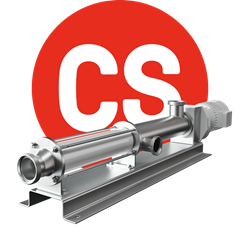
CS - FOOD AND HYGIENIC PUMPS
In areas with sensitive hygienic requirements, cleanliness is a critical factor. SEEPEX food and hygienic pumps fulfill even the strictest hygiene requirements in the food, pharmaceutical, cosmetics and chemical industries, conveying both high- and low-viscosity substances with minimal shear effect. They ensure product quality at all times in compliance with 3-A Sanitary Standards.
The components of our food and hygienic pumps are designed in compliance with EHEDG principles. The BCFH range even has certification to mark it as particularly hygienic and easy to clean. All materials in contact with the pumping product naturally fulfill the international requirements of the FDA and EU 1935-2004.
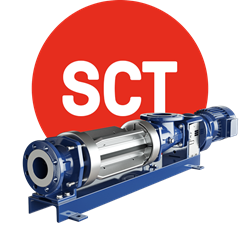
SCT - SMART CONVEYING TECHNOLOGY
The patented Smart Conveying Technology (SCT) ensures the fastest maintenance possible resulting in reduced downtime and significantly reduced life cycle costs in virtually all market sectors. The Smart Stator and Rotor are both manufactured in two pieces allowing the pump to be maintained without the need to remove either the suction or discharge pipe work resulting in an 85% reduction in maintenance times.
The unique design of SCT enables the sealing line between the rotor and stator to be adjusted to suit the required application and also to compensate when wear starts to occur, typically resulting in more than doubling the life of the rotor and stator.